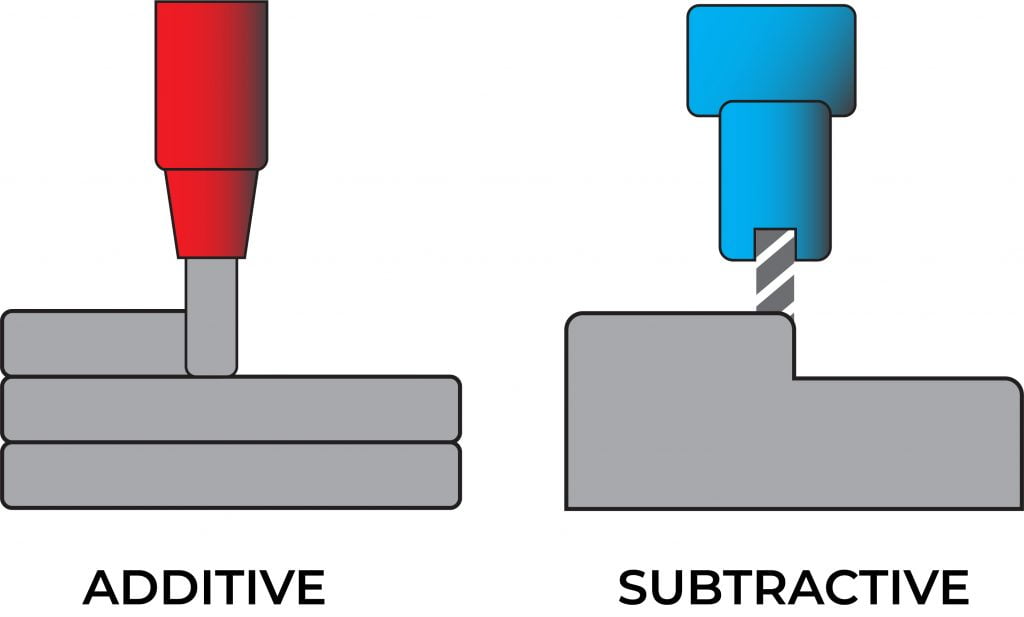
For entrepreneurs creating a product for the first time, it can be daunting to learn the jargon. First-timers already have much on their plate, and seasoned entrepreneurs can always use a refresher. Today, we are discussing additive and subtractive manufacturing. These terms often arise when prototyping products and later when you move forward with batch manufacturing. Once you learn the differences, similarities, and how factories utilize both, it will be easy to remember. Adding more manufacturing vocabulary to your toolbox will be a great asset on your journey to making quality products. Enjoy!
Additive and subtractive manufacturing are methods for developing products within a supply chain. Let’s explore the value of their similarities and differences and understand how they are combined.
Additive Manufacturing
Additive manufacturing, also known as 3D printing, is gaining popularity while subtractive manufacturing has existed. Manufacturers utilize additive manufacturing for short-run and custom parts, objects that do not require a smooth finish and replicating complicated designs. Additive manufacturing streamlines the prototyping process using computer software-generated models, which direct a 3D printer to create the item by adding material layer by layer. The materials range from metal alloys and thermoset polymers to thermoplastics. Underneath additive manufacturing are different techniques like sheet lamination, binder jetting, and material extrusion. The cons are that there is a limited range of materials, which is only ideal for small quantities. The pros of additive manufacturing are that it creates minimal waste, is faster, and can handle complex designs.
Subtractive Manufacturing
Subtractive manufacturing requires cutting away material from blocks of metal or plastic. Then the CNC or Computer Numerical Control software directs the machine to remove or subtract the appropriate material from the block to create the product. Some possible materials include metals, Nylon, PVC, plexiglass, and wood. CNC does this in a few ways, including lasers, cutting, and water. Subtractive manufacturing is for the mass production of homogenous parts. The cons are that it creates more waste, takes more time, and is generally more expensive than additive manufacturing. The pros of subtractive manufacturing are that it applies to various materials, is used for all shapes, creates a smooth surface, and is highly accurate.
Combining
Manufacturers combine additive and subtractive manufacturing to compensate for each one’s shortcomings. For example, they can create elaborate prototypes with a 3D printer or additive manufacturing and create different finishes with subtractive manufacturing.
Contact
Thank you for supporting us. Do you have questions about additive or subtractive manufacturing? Reach out to Rad Sourcing today!